Electrospinning Technique for Creating Effective Filters Against Pathogens
Posted: 30 June, 2025
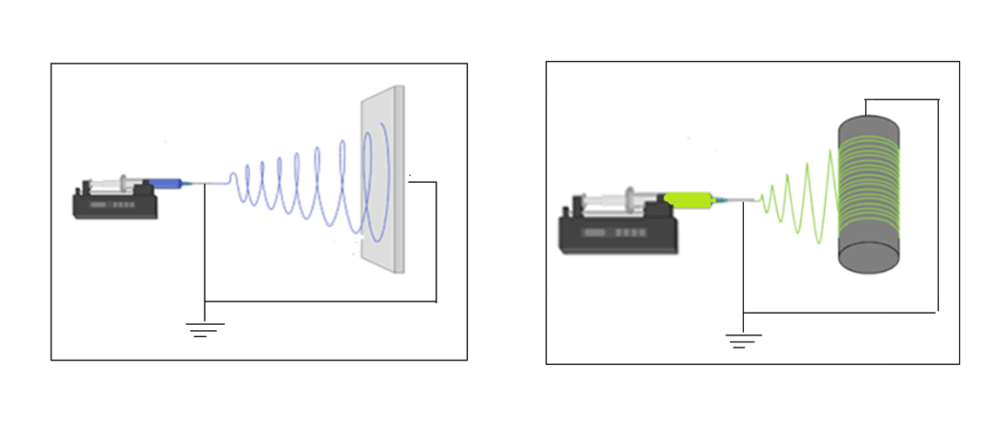
Electrospinning is a sophisticated manufacturing technique that facilitates the production of non-woven fibrous structures, featuring fibre diameters ranging from 1nm to 10 micrometres, depending on the electrospinning setup. The main advantage of this technique is its ability to integrate various types of functional materials into fibre membranes. This capability allows for the customization of properties to meet specific needs across a range of applications, including functional surfaces, drug delivery systems, and filtration processes (Figure 1). Nanofiber membranes for controlling airborne viruses demonstrate excellent performance in capturing bacteria-laden virus aerosols due to their pore size, porosity, and retained charge [18-19].
During the electrospinning process, regulation of processing parameters is essential to obtain proper nanofiber membrane. These factors have a direct impact to tune critical characteristics of the produced membranes for the effective filtration process such as fibre diameters, surface morphology, and overall texture [18, 19].
In our electrospinning experiments, poly (vinyl alcohol) (PVA Mw 89,000-98,000; 99% hydrolysed) was used as polymer. Different concentration to produce nanofibers with and without base layer was tested and the best results was obtained with 10% PVA solutions. We used 10mL syringe with metal needle that filled with PVA solution, and the solution was released by the syringe pump at a flow rate of 1.00 mL/h. When the high voltage (16kV) was applied between the syringe tip and the plate collector (covered with aluminium foil), the polymer is ejected from the syringe tip and gets deposited on the collector and base layer respectively (Figure 2a).
The morphology of the electro spun membranes was observed using Scanning Electron Microscope (SEM) (Zeiss Sigma 300). ImageJ software was used to determine the average fibre diameter by taking the average of measurements taken at random places for each nanofiber. The SEM micrographs showed that nanofiber membranes obtained from 10 % (wt.) PVA solution gave good results, and uniform nanofiber membranes was obtained with fibre diameter of about 1 micrometre (Figure 3a). However, to ensure that the nanofiber retains its structural integrity and to enhance its processability for coating application, incorporation of nanofiber membranes with a nonwoven base layer was chosen. This layer serves not only to reinforce the nanofiber membrane but also to facilitate its handling and application during the spray coating process, ultimately leading to a more robust and effective final product. However, the surface morphology of the nanofibers collected on the base layer exhibited significant irregularities, leading to suboptimal shapes and structures (Figure 3b).
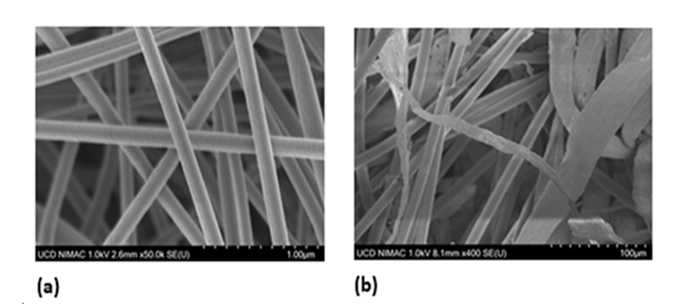
The electrospinning setup was modified to incorporate a rotating drum collector in place of the previously used stationary flat collector (Figure 2b). This modification significantly enhanced the adhesion of nanofibers to the base layer, resulting in a more uniform distribution of fibers across the membrane. Additionally, the dynamic movement of the drum during the electrospinning process improved the surface morphology of the electrospun membranes by promoting fiber alignment and reducing imperfections. These enhancements contributed to the overall mechanical and functional properties of the final product, as illustrated in Figure 4. The applied voltages during the electrospinning process were increased from 16 kV to 22 kV, allowing for a more refined control over the fiber diameter and morphology. Concurrently, the concentration of the polyvinyl alcohol (PVA) solution was elevated from 10% (weight/weight) to 14% (weight/weight). This adjustment in concentration aimed to improve the viscosity of the solution, thereby enhancing the stability of the electrospinning jet and facilitating the production of uniform nanofibers with the diameter between 0.74µm to 1.1µm. To significantly enhance the durability and mechanical strength of the nanofiber membranes, a curing process was implemented at a controlled temperature of 120°C for a duration of 2 hours. This thermal treatment allows for optimal polymer cross-linking, resulting in improved resistance to environmental factors and extended lifespan of the membranes in various applications.
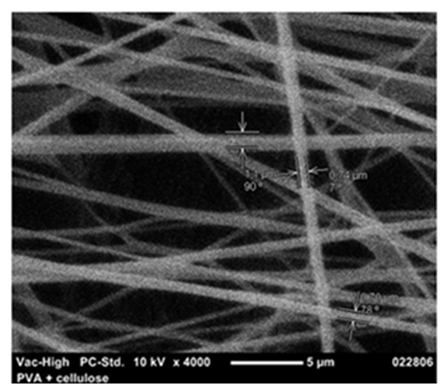
The research will involve comprehensive characterization tests of the produced nanofiber membranes to evaluate their structural, mechanical, and thermal properties. In addition, the study will focus on the functionalization of these nanofiber membranes by incorporating cationic polymers. This process aims to enhance their antimicrobial activity and improve their ability to capture contaminants.